Kaizen - to ludzie
- Jak zaangażować zespół w programy usprawnień pracowniczych?
- Na czym polega cykl Deminga?
- Dlaczego kaizen w firmach często nie przynosi oczekiwanych rezultatów?
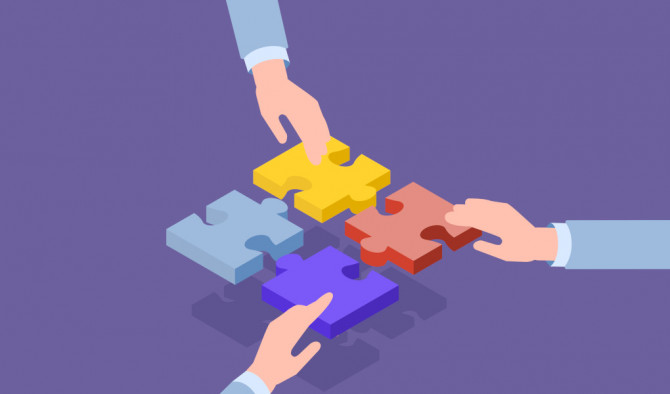
Zaskakuje mnie, jak niewiele przedsiębiorstw decyduje się na wprowadzenie u siebie idei kaizen. Jeszcze bardziej zaskakuje mnie, w jak wielu firmach, w których ją wdrożono, nie działa. Przyczyn jest wiele, podobnie jak teorii na ten temat. Z moich obserwacji wynika, że najczęściej pracodawca zapomina, że kaizen to ludzie.
Żeby kaizen przynosiło korzyści dla firmy, potrzebni są pracownicy – zaangażowani, zadowoleni i doceniani. Chciałbym podzielić się moimi obserwacjami i przemyśleniami dotyczącymi zaangażowania ludzi w programy usprawnień pracowniczych.
Początki ciągłego ulepszania pracy (TWI)
Nazwa kaizen sprawia, że naturalnie kojarzymy ją z Japonią. Warto jednak wiedzieć, że idea „drobnych kroków” nie jest pradawną sztuką opracowaną w czasach samurajów. Jej zalążki powstały w latach 40. XX w. w Stanach Zjednoczonych1. Gdy w maju 1940 r. Niemcy rozpoczęły inwazję na Francję, Amerykanie zrozumieli, że II wojna światowa jest nieunikniona. Dobrze wiedzieli, że jeżeli nastąpi konieczność przystąpienia amerykańskich wojsk do działań wojennych, to do armii zostanie powołana większość mężczyzn w wieku produkcyjnym, którzy pracowali głównie w przemyśle. Opracowano więc program TWI (ang. Training Within Industry), który rozwijał umiejętności zarządcze wśród doświadczonych pracowników operacyjnych oraz przełożonych niższego i średniego szczebla. W program TWI osobiście zaangażowany był William Edward Deming, znany jako człowiek, który wymyślił koło.
Wielu czytelników na pewno kojarzy koło lub cykl Deminga: Plan – Do – Check – Act. Jest to niezwykle skuteczna zasada ciągłego ulepszania, która była z powodzeniem wykorzystywana w jednym z filarów TWI – umiejętność doskonalenia metod pracy. W trakcie działań wojennych presja czasu sprawiała, że wszyscy pracownicy musieli być zaangażowani w wynajdowanie drobnych sposobów poprawiania jakości wyrobów i zwiększania efektywności ich wytwarzania. Kierownicy zobowiązani byli, aby każdy pomysł traktować z należytym szacunkiem. Początkowo to podejście mogło wydawać się szokujące, jednak strategia małych kroków przyczyniła się do niezwykłego wzmocnienia zdolności produkcyjnej USA. Niestety, gdy wojna się zakończyła i żołnierze powrócili do domu, a produkcja zaczęła wracać do normy, strategie związane z TWI zaczęły być ignorowane.
TWI fundamentem dla lean management
Tymczasem w pokonanej Japonii sytuacja gospodarcza była zgoła odmienna. Brak efektywności w produkcji i niskie morale pracowników skłoniły generała Douglasa MacArthura – przywódcę sił okupacyjnych – do ściągnięcia specjalistów od TWI. Uważał on, że poprawa japońskiej gospodarki leży w jego najlepszym interesie, gdyż tylko silne społeczeństwo będzie w stanie stawić czoła potencjalnemu zagrożeniu ze strony Korei Północnej oraz zapewnić zaopatrzenie jego wojskom. Przeprowadzono kurs zarządzania dla japońskich biznesmenów – MTP (Management Training Program), który był prawie identyczny z tym opracowanym przez Deminga i jego kolegów. W szkoleniu wzięły udział tysiące japońskich przedsiębiorców. Japończyków najbardziej interesowały informacje dotyczące produkcji w Stanach Zjednoczonych, gdyż uważali, że to rozwój produkcji miał największy wpływ na przewagę technologiczną Amerykanów, a co za tym idzie – na ich zwycięstwo. Japończycy szybko przyswoili wiedzę i nigdy nie zaniedbali jej jak Amerykanie – a wręcz zaczęli ją rozwijać. To ona położyła fundamenty pod lean management i m.in. kaizen – zmiany na lepsze.
Wykorzystałeś swój limit bezpłatnych treści
Pozostałe 77% artykułu dostępne jest dla zalogowanych użytkowników portalu. Zaloguj się, wybierz plan abonamentowy albo kup dostęp do artykułu/dokumentu.